铸铜鼎在铸造过程中容易出现哪些缺陷,如何避免这些缺陷
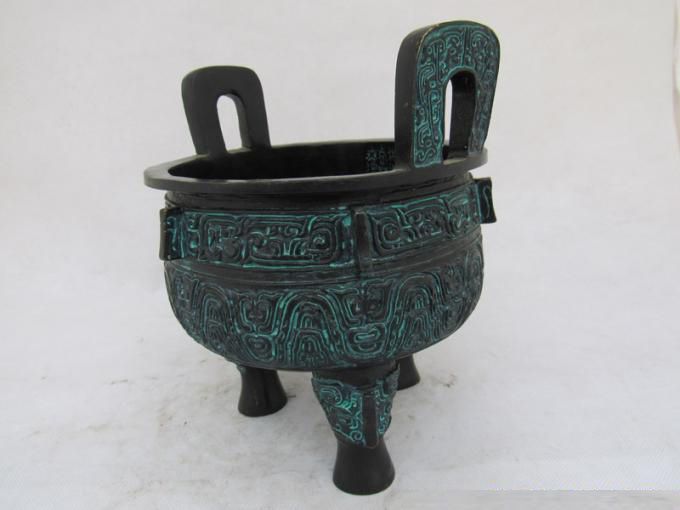
在铸铜鼎的铸造过程中,常见的缺陷有气孔、缩孔、砂眼和裂纹等。气孔是由于在铜液浇铸过程中,气体未能及时排出,在铸件内部形成的空洞。其产生原因主要有铜液熔炼时未充分除气,模具透气性不佳等。为避免气孔,在熔炼铜液时,可采用吹气搅拌等方式充分去除铜液中的气体,同时在模具制作时,合理设置排气通道,确保气体能够顺利排出。例如在制作模具时,在易产生气孔的部位设置细小的通气孔,或者在模具表面涂抹一层透气材料。缩孔是因为铜液在冷却凝固过程中体积收缩而形成的孔洞,通常出现在铸件的厚壁部位或热节处。要防止缩孔,可通过优化铸件的结构设计,使壁厚均匀,减少热节的产生。在铸造工艺上,采用顺序凝固原则,设置冒口,让铜液从远离冒口的部位开始凝固,逐渐向冒口方向推进,使冒口最后凝固,从而将缩孔转移到冒口处,最后切除冒口即可。比如在设计铜鼎时,对较厚的耳部等部位进行适当的减薄处理,或者在厚壁处增加散热筋,加快冷却速度。砂眼是由于型砂或芯砂在铸造过程中脱落,混入铜液中,在铸件表面或内部形成的孔洞。为防止砂眼,要提高型砂和芯砂的质量,增强其强度和耐火性,减少砂粒的脱落。同时,在合模和浇铸过程中,要避免型砂受到冲击和破坏。例如在制作模具时,对型砂进行充分的紧实处理,并且在浇铸前仔细检查模具,清理模具内的浮砂。裂纹分为热裂纹和冷裂纹。热裂纹是在铜液凝固过程中,由于收缩应力过大而产生的;冷裂纹则是在铸件冷却到较低温度时,因内应力过大引发。防止裂纹,需要在铸造过程中控制好冷却速度,避免过快冷却产生过大的应力。同时,优化铸件的结构设计,减少应力集中的部位。例如在铜鼎的耳部与主体连接部位,采用过渡圆角等设计,降低应力集中。